
Our Processes
All our Remanufacturing is done right here in Langley.
Quality starts at the core. Gears are first cleaned in our environmentally friendly parts washer and then blasted in our automated sandblaster. The gear (if suitable for rebuilding) is dismantled, and all parts are re-washed and cleaned again, before being examined and measured to ensure that the parts are within tolerances. Contact us to learn more about our remanufacturing process in Langley.
​
Please note that fully 60% of all pitman shafts are discarded due to pitted seal surfaces or worn teeth. We use only new shafts.

All valves are totally dismantled and checked for wear, and their internal seals are always replaced. Other rebuilders will pre-test gears to avoid this time-consuming step in the rebuilding process. However, we remanufactured gears to the OEM specifications, and we long ago determined that it was one of the most necessary steps to avoid input seal leaks and torsion bar weeps.
As the gear is being reassembled, all critical safety procedures are checked and then double-checked by another technician. No chances are taken as safety is paramount and “good enough” won’t do. All seals are replaced as the gear is being rebuilt. All adjustments and settings are performed by the technicians who have serviced literally thousands of gears.
Our Testing Process
When we sell a steering gear, we need to know that it will perform safely and correctly for an extended period of time, and will generate for us yet another satisfied customer. To achieve this, we have a test system that mimics the real-world driving conditions as closely as possible.
​
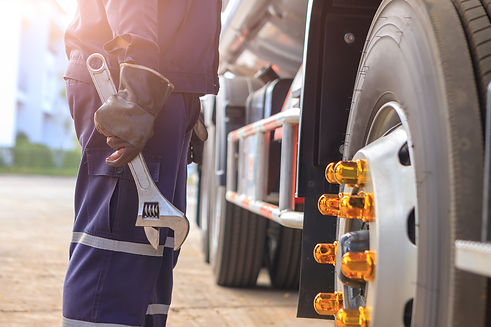

-
The first part of the test is a simple check for leaks under no-load conditions.
-
The second test is to increase the flow to 150% of the normal to check valve balance.
-
The third test is to cycle the gear many times to check for smooth operation, stiffness, or binding.
-
The fourth test is performed under load and checks for internal bypass, correct poppet operation, and correct steering effort at the recommended pressure and flow.
When the gear has passed all tests, it is sealed with the port plugs, then painted and placed into the stock.
Our Commitment to the Planet
Remanufacturing something to make it serviceable again is absolutely the most environmentally friendly way of producing a useable product while saving the planet many tons of carbon in steel production, hundreds of man-hours of machining involving energy use and thousands of barrels of oil, transporting it from the raw state to a finished product.
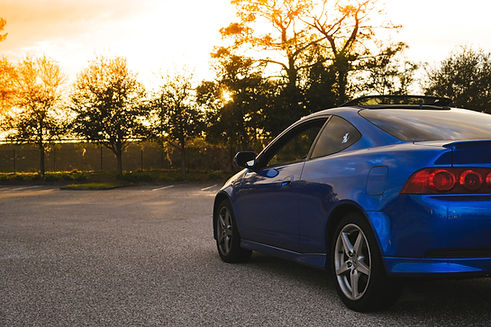

Our entire operation recycles everything possible. We spend thousands of dollars each year to have waste oil, solvent tank fluid, and waste parts washer water disposed of safely and properly. Even our shipping boxes are made from recycled cardboard, and if still clean and useable again they will have a second life as packing in new product shipping!
We are all responsible for our environment, and we do our utmost to ensure our business is part of the solution and not part of the problem!
